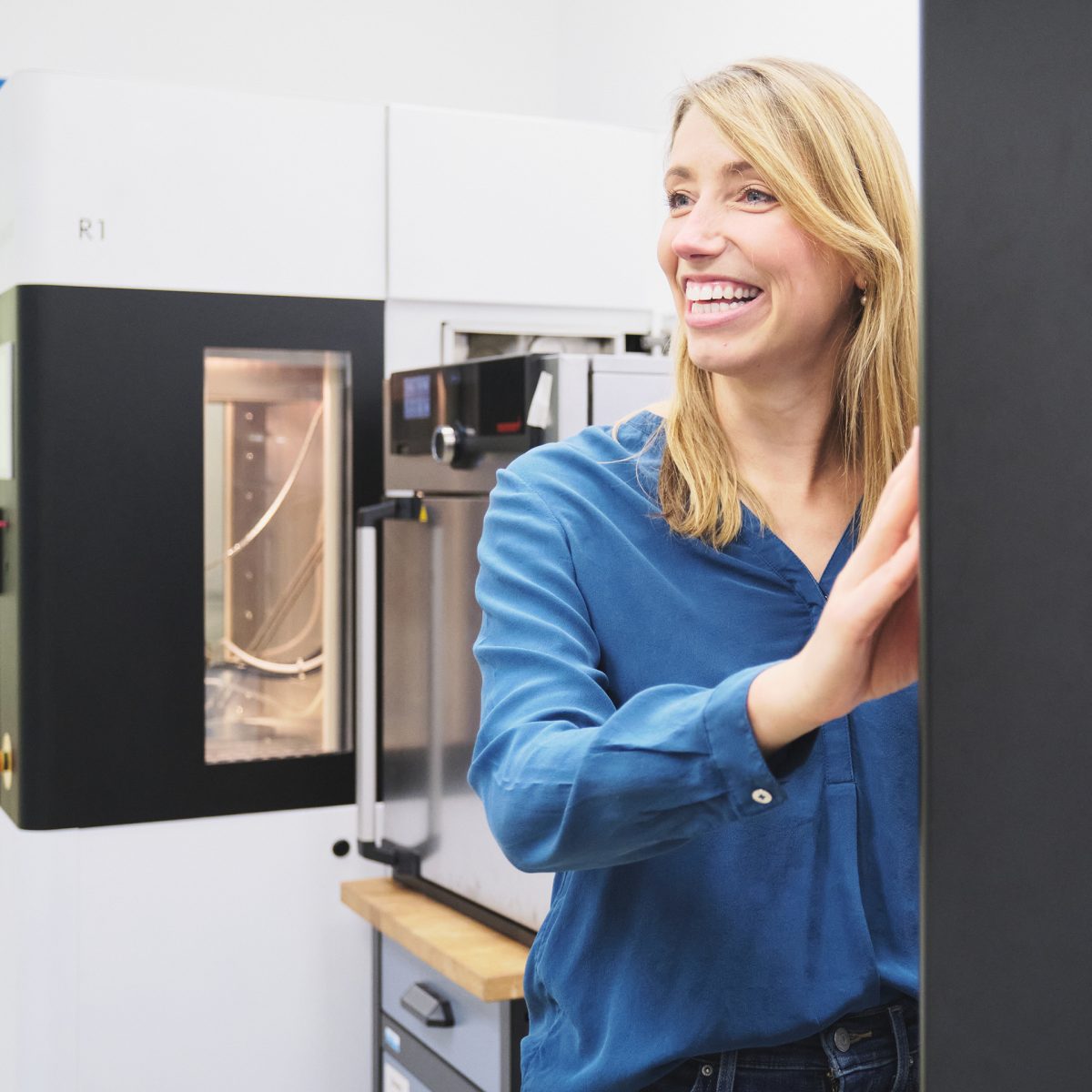
Together with her fellow founders, TUM alumna Miriam Haerst has developed a 3D printer that makes it possible to produce plastic implants and surgical aids with a precise fit (Image: Alexander Gerner/TUM).
And yet, for a long time, she found it hard to imagine studying Natural Sciences – and especially pursuing a Doctorate. She thought it would be too theoretical and not practical enough. Nevertheless, a year before her high school graduation, she attended the Herbstuni at TUM. This is a program specifically for schoolgirls, offering various courses in which, for example, they can program a robot or build bridges and learn about mechanics, trusses and force transmission. Being able to jump directly into hands-on experience and test the application of theoretical concepts appealed to Miriam Haerst and convinced her to enroll in Mechanical Engineering at TUM.
BONES FROM A 3D PRINTER
Today, she is the CEO of her own company and, together with her fellow founders – all four of whom are also TUM Alumni – has developed a 3D printer that makes it possible to produce plastic implants and surgical aids with a custom fit. The 3D printer, called Kumovis R1, has roughly the dimensions of a large refrigerator and can generate heat of up to 250 degrees Celsius. Together with hospitals and manufacturers of medical devices, the start-up is producing implants from high-performance polymers by using the 3D printer to apply the material layer by layer. The implants can be used to replace skull and facial bones, but also printed intervertebral disc replacements are conceivable.
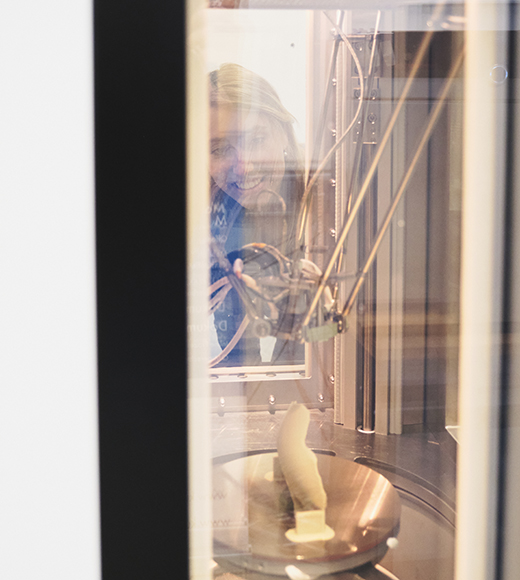
Founder Miriam Haerst looks into the interior of Kumovis' 3-D printer, where a bone implant is currently being produced (Photo: Alexander Gerner/TUM).
“It’s probably part of my personality that I can’t get hung up on simulation to the last detail, but I have to get into trial and error pretty quickly.”
UNCONVENTIONAL THINKING
Talking about her time at TUM today, she emphasizes how much she enjoyed the free thinking at the Chair of Medical Engineering. “We were given the opportunity to think in all kinds of directions, to develop ideas and directly put them to the test,” she says. Even the foundations for the technology of her 3D printer were developed in a project seminar during her Doctorate.
Der 3-D-Drucker namens Kumovis R1 hat etwa die Dimensionen eines großen Kühlschranks und kann bis zu 250 Grad Celsius an Hitze erzeugen. Er produziert Implantate aus Hochleistungspolymeren, indem der 3-D-Drucker das Material Schicht für Schicht aufträgt (Bild: Alexander Gerner/TUM).
Finally, the five founders came up with the idea of trying a circulating air flow – similar to an oven with circulating heat. This was a decisive leap forward in development, because it meant that the air could also be filtered at the same time. “We didn’t stick with the old and instead consciously decided on a new approach,” Miriam Haerst reports. For this path, she was honored as one of the best innovators under 35 in 2019. “To be truly creative and develop solutions for existing problems, you have to think unconventionally and outside the box,” she is convinced. Experimenting with new things together as a team is her preferred method for doing so. “I always make sure to give us freedom as a team to spin ideas and to experiment. You never know what you’ll discover in the end.”
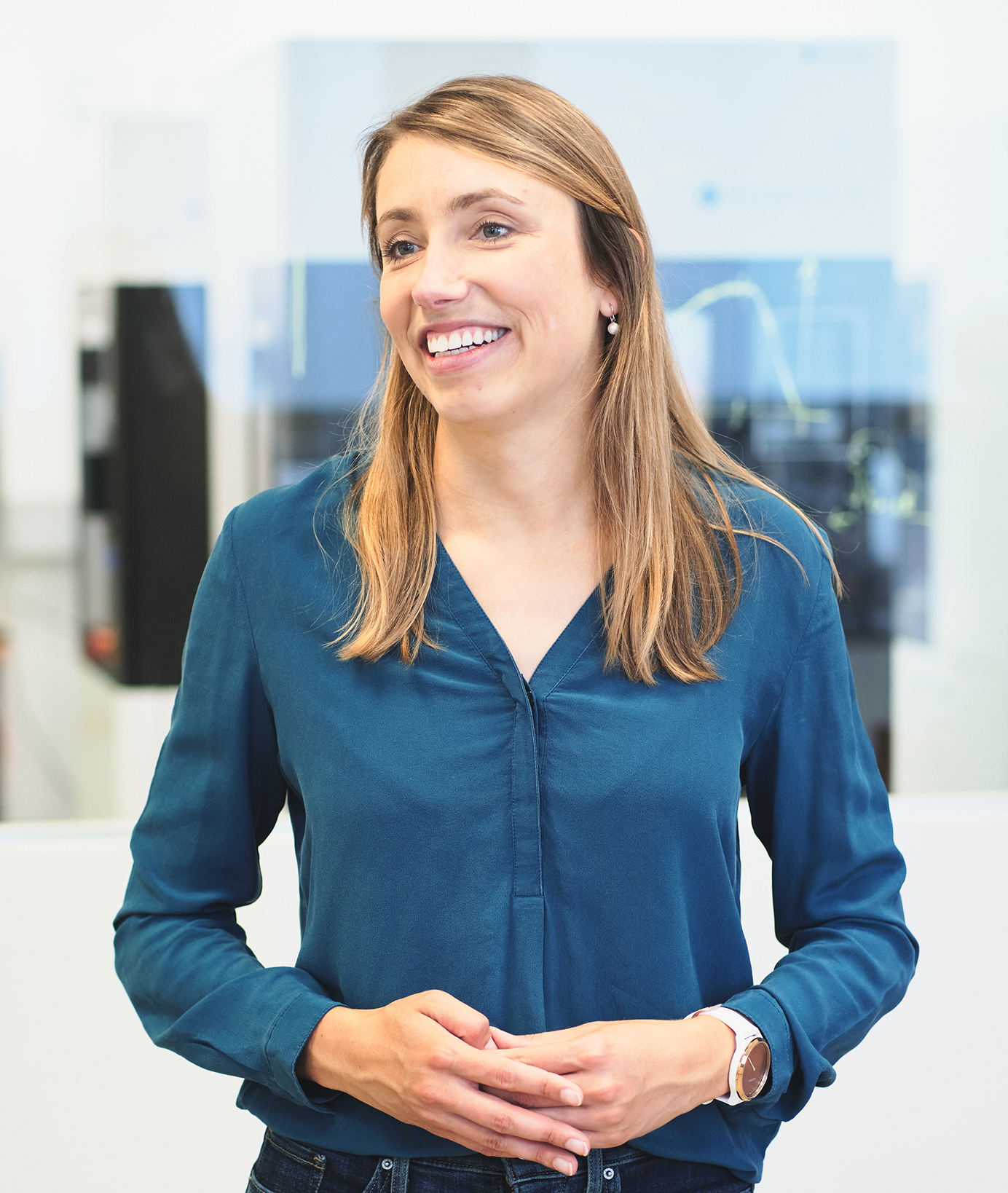
Picture: Alexander Gerner/TUM.
Diploma Mechanical Engineering 2011, Doctorate 2016
Still a student of Mechanical Engineering at TUM, Miriam Haerst gained her first experience in 3D printing while working for a manufacturer of hearing aids. During her Doctorate and work at the Chair of Medical Engineering at TUM, she focused on the processing of plastics for medical applications and the effects of a medical environment on plastics.
In a project seminar, she worked together with TUM Alumni Stefan Leonhardt, Stefan Fischer, Sebastian Pammer and Alexander Henhammer on a 3D printer for the high-performance polymer PEEK. After its first laboratory samples, it was clear that the group would keep at it for further development.
In 2017, Miriam Haerst co-founded the start-up Kumovis – with the help of TUM Start-up Consulting and an EXIST research transfer funding project from the German federal government. Kumovis currently has 25 employees, successfully completed its Series A financing round last year, and raised 3.6 million. This year, a subsidiary in the US was set up, Kumovis Inc.